Auf Grundlage der gegenseitigen Übereinstimmungen zwischen SDIL und SmartFactoryKL, haben wir für eine Zusammenarbeit mögliche Forschungsfelder identifiziert, die beiden strategischen Forschungszielen entsprechen. Die diesbezüglich geführten Gespräche haben einer Vision den Weg bereitet, die in einem engen Zusammenhang steht mit den aktuell wiederholt aufkommenden Forschungsthemen „Industrie 4.0“ und „Internet der Dinge“. Sie fällt damit in den Kompetenzbereich der Echtzeitdaten-Integration und des Wissensmanagaments. SmartFactoryKL wird als realitätsnähe Plattform zu Forschungs- und Demonstrationszwecken genutzt. Als eine herstellerunabhängige Demonstrations-und Forschungsplattform ist die SmartFactoryKL in dieser Form einzigartig in Europa. Hier werden innovative Informations-und Kommunikationstechnologien und deren Anwendungsmöglichkeiten in einer realistischen industriellen Produktionsumgebung getestet sowie weiterentwickelt.
Produktionsanlagen sind durch eine Reihe von Maschinen gekennzeichnet, die typischerweise einige Waren in aufeinanderfolgenden Bearbeitungsschritten in einer Fertigungsstraße herstellen. Jeder dieser Bearbeitungsschritte greift auf verschiedenen Maschinen und Werkzeugen zurück, die für ihre spezifische Aufgabe individuell angepasst sind. Das problemfreie Funktionieren der eingesetzten Maschinen wiederum ist abhängig von Umweltparametern, wie Spannung, Druck, Temperatur etc. Diese werden üblicherweise messtechnisch überwacht mittels Anzeigen, Kontrolllampen etc. Eine große Anzahl von Sensoren, die kontinuierlich die für den Produktionsprozess relevanten Statusinformationen zur Verfügung stellen, ist demnach charakteristisch für moderne Maschinen, die das Paradigma des „Internets der Dinge“ (IoT) zufriedenstellend erfüllen. Die Sensoren können überwacht, Alarme beim Überschreiten bestimmter Schwellenwerte ausgelöst und so der laufende Produktionsprozess angehalten werden, bis ein Ingenieur den Defekt behoben hat. Allerdings ist die Beschaffenheit der meisten Sensoren wesentlich komplizierter. Ihre Werte variieren über die Zeit selbst im Normalbetrieb und eine Fehlfunktion ist nicht einfach anhand überschrittener Schwellwerte zu ermitteln, sondern erfordert eine Zeitreihenanalyse und die Identifizierung von Ausreißern bzw. Sonderfällen. Dennoch besteht ein großes wirtschaftliches Potenzial hinsichtlich der Beobachtung und Analyse solcher Sensoren. Bereits kleinste Abweichungen dieser dynamischen Werte von den erwarteten Sollwerten kann durch den sogenannten Butterfly Effekt zu einem erheblichen Qualitätsverlust der produzierten Ware führen. Eine intelligente Überwachung, Speicherung und Analyse der Sensordaten kann vielfache positive Auswirkungen haben:
- Die Zeitreihenanalyse für alle Sensoren in einer Produktionslinie unter normalen Bedingungen ermöglicht das Trainieren eines Erkennungsalgorithmus für Anomalien. Derart trainierte Algorithmen können die Gesamtsystemleistung deutlich besser klassifizieren als manuelle Regeln für eine Auswahl von Sensoren und ihre erwarteten Sollwerte.
- Die Archivierung von Maschinendaten zur späteren Referenz und Analyse kann sehr viel effizienter sein, da nur als „nicht normal“ klassifizierte Zustände gespeichert werden müssen.
- Der Abruf solcher außerordentlichen Bedingungen innerhalb von Datenprotokollen für eine spätere Analyse ist einfacher. Denn es können nicht nur Zeitmarken, sondern auch erklärbare Voraussetzungen, die zu den Ausreißern geführt haben, genutzt werden, um die Daten zu indexieren.
- Die Ware, die von den Ausreißer-Bedingungen während der Produktion beeinträchtig wurde, kann mittels ihrer Seriennummer identifiziert werden – sofern Seriennummern zur Indexierung der (Ausreiser-)Sensordaten verwendet werden.
- Auftretende Ausreißer können im Zuge der Live-Überwachung erkannt werden, was ein wesentlich effizienteres und schnelleres Eingreifen ermöglicht und dadurch zu weniger Ausschuss bei der produzierten Ware sowie einer Kostenoptimierung führt.
- Eine langfristige Optimierung der Ausreißer-Erkennung: Ware die unter Ausreißer-Bedingungen produziert wurde, aber keine erheblichen Mängel in ihrem Halbzeit-Produktlebenszyklus aufweist, kann dazu dienen, die Bedingungen als „normal“ zu akzeptieren, wodurch der Anomalie-Erkennungsalgorithmus lockerer wird.
- Andererseits kann Ware, die zu früh in ihrem Produktlebenszyklus kaputtgeht und unter Ausreißer-Bedingungen zustande kam, dazu genutzt werden, die Bedingungen für einen zukünftigen Produktionsstopp zu schärfen/zu erhöhen. Dadurch werden eine Verringerung von Garantiefällen und eine weitere Kostenoptimierung ermöglicht.
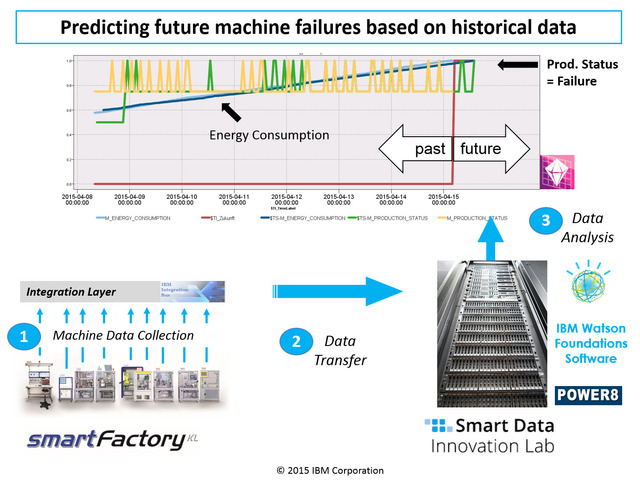
Die angestrebte gemeinsame Forschungsarbeit, die mit diesem Projekte durchgeführt werden soll, befasst sich mit prototypischen Untersuchungen bzgl. der oben angesprochenen Aspekte. Die im Rahmen des Projekts verwendeten Sensordaten werden aus der Produktionslinie der SmartFactoryKL extrahiert, und gleichen somit realen Daten, die folgende Informationen enthalten:
- Modulinformationen, z.B. Energieverbrauch, Betriebsstunden, Produktionsstatus
- Produktinformationen (über Auftrag, Kunde, Priorität)
- Topologie-Informationen (Nachbarn rechts/links, Port IDs)
- Prozessinformationen (Bearbeitungszeit, Energie)
- Transportinformationen (Transportstatus, Fehler, etc.)
Die Fertigungsstraße der SmartFactoryKL besteht aus fünf anbieterspezifischen Stationen bzw. Modulen, die der Herstellung eines exemplarischen Produkts dienen: einem kundenspezifischen Visitenkartenhalter. Der Montageprozess beginnt am Gravur-Modul. Zunächst werden aber alle kundenspezifischen Auftragsdaten auf das Produktgedächtnis geschrieben. Das Produkt selbst trägt diese Information über den gesamten Produktlebenszyklus hinweg. Das digitale Produktgedächtnis wird über einen RFID-Transponders realisiert, der in die Grundplatte eingebaut ist. Das Gravur-Modul entlädt die Bodenplatte des Visitenkartenhalters (mit dem Fertigungsauftrag) und bringt mit einer CNC-kontrollierten Miniatur-Fräsmaschine eine individuell an den Kundenwunsch angepasste Gravur darauf auf. Daraufhin wird die gravierte Grundplatte gedreht und auf einem Werkstück platziert, das diese an das nächste Produktionsmodul übergibt. Die nächsten beiden anbieterspezifischen Module übernehmen das Anbringen einer Halteklammer am Boden des Visitenkartenhalters und den Zusammenbau verschiedenfarbiger Gehäuse-Elemente. Ein Roboter setzt den kundenspezifischen Deckel auf die Grundplatte und presst die beiden Teile zusammen. Ein weiteres Modul appliziert mit einem Laserbeschriftungssystem einen individuellen 2D-Strichcode auf der Oberseite des Visitenkartenhalters. Das letzte Modul übernimmt zwei verschiedene Aufgaben: die Endkontrolle des Produkts mittels einer hochauflösenden Kamera sowie die Ausgabe des fertigen kundenspezifischen Visitenkartenhalters. Vor und nach jedem Bearbeitungsschritt wird das Produktgedächtnis gelesen und via RFID aktualisiert. Module können während des Anlagebetriebs leicht entfernt oder hinzugefügt werden, was die Möglichkeit eröffnet, das Fertigungsmodul des Anbieters auszuwählen, dessen Expertise am besten für die jeweiligen Erfordernisse geeignet ist.
Für eine zukünftige Weiterentwicklung solcher hochmodulare, Multi-Anbieter-Produktionssysteme ist es erforderlich, die Daten in allen Entwicklungsstadien zu überwachen, zu kontrollieren und zu verarbeiten. Übergeordnete IT-Systeme müssen für diesen Zweck einen kontinuierlichen Zugriff auf die Daten haben. Schlüsseltechnologien zur Ermöglichung einer vertikalen Integration innerhalb dieser Anlagestruktur sind die Kommunikationsstandards OPC UA und der integrierte Web-Server. Der in jedem anbieterspezifischen Modul integrierte OPC UA Server garantiert die reibungslose Interaktion verschiedener Module über Herstellergrenzen hinweg. Auf diese Weise werden Informationen bzgl. der Anlagentopologie und dem werkstückspezifischen Energieverbrauch sowie Statusmelden direkt an übergeordnete IT-Systeme übertragen. All diese realen Daten, die die oben erwähnten Informationen enthalten, können vom SDIL genutzt werden. Die breite Anwendung von Komponenten der Zukunftsindustrie 4.0. erfordert neue Qualifikationen über die nächsten Jahre. Prädiktive Instandhaltung wird eines der Schlüsselthemen sein und soll im Rahmen dieses Projekts in Angriff genommen werden.
In Zusammenarbeit mit dem Partner IBM, plant SmartFactoryKL die Durchführung eines gemeinsamen Projekts mit dem Smart Data Innovation Lab. Das Projekt staffelt sich in folgende drei Phasen:
- Die Smartfactory KL hat dem SIDL ca. 20 GB generierte Daten zur Verfügung gestellt, die ein bestimmtes Problem in der Vergangenheit replizieren: nämlich ein beobachteter sporadischer Motorausfall bei mehreren Modulen. Problem wurde letztlich auf den Kontakt der Montagebänder zweier benachbarter Module zurückgeführt. Es handelt sich hierbei um ein in der SmartFactoryKL demonstriertes Szenario, das eine quantitative Extrapolation durch das SDIL darstellt, unter Verwendung der gleichen Analysemethode und Technologie bei der Skalierung.
- Bis zur HMI 2016: In Vorbereitung auf die HMI wird die SmartFactoryKL Belastungstests zur Stabilitätssicherung der Anlage durchführen. Es werden enorme Daten (und Fehler) generiert werden, die dann dem SDIL übergeben und analysiert werden. Die Ergebnisse werden zurückgemeldet, um die Qualität der Demonstrationsanlage zu verbessern.
- Es erfolgt eine Weiterführung der Forschungsarbeit, um verschiedene Strategien der Datenerfassung, Analysemethoden sowie Geschäftsmodelle im Bereich der vorausschauenden Wartung, OEE und Qualitätssicherung im Produktionskontext zu identifizieren.
“Gemeinsam mit dem SDIL und der IBM Watson Foundation untersuchten wir im Frühjahr 2015 IoT-Potenziale für smarte Fabriken der Zukunft”, sagt Rüdiger Dabelow, Mitarbeiter beim SmartFactory Laboratory des DFKIs. “Es wurden Möglichkeiten des Internets der Dinge für die Produktion und Fertigung ausprobiert und getestet.”
Data Innovation Community
Industrie 4.0
Projektpartner
Technologie-Initiative SmartFactory-KL e.V., DFKI, IBM
Ansprechpartner
Plamen Kiradjiev, kiradjiev@de.ibm.com
Dominic Gorecky, dominic.gorecky@dfki.de
Zeitraum
Nov. 2015 – Juni 2016